WPC Total Solution Whole Plant Equipment
WPC Materials Main Production Process Flow
WPC Pulverizing + Mixer System
In the production process of Wood Plastic Composite (WPC), natural fiber can mix with 30%-80% of the polymer. Therefore, the selection of natural fiber (sawmill, chipboard, rice husk, etc.) is important. All natural fiber must pulverize as 40mesh~120mesh of particle size.
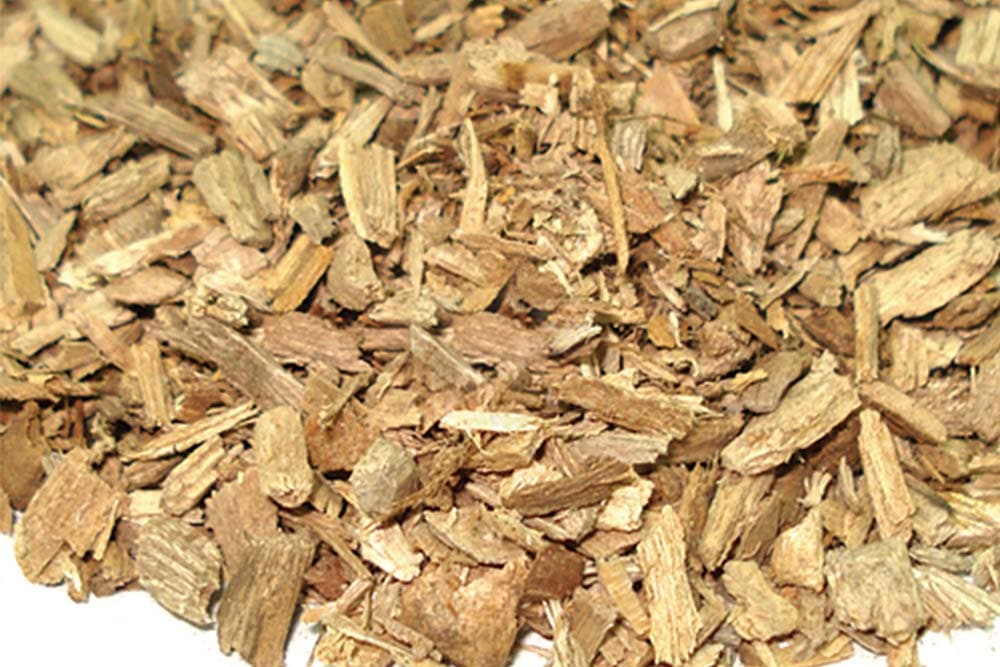
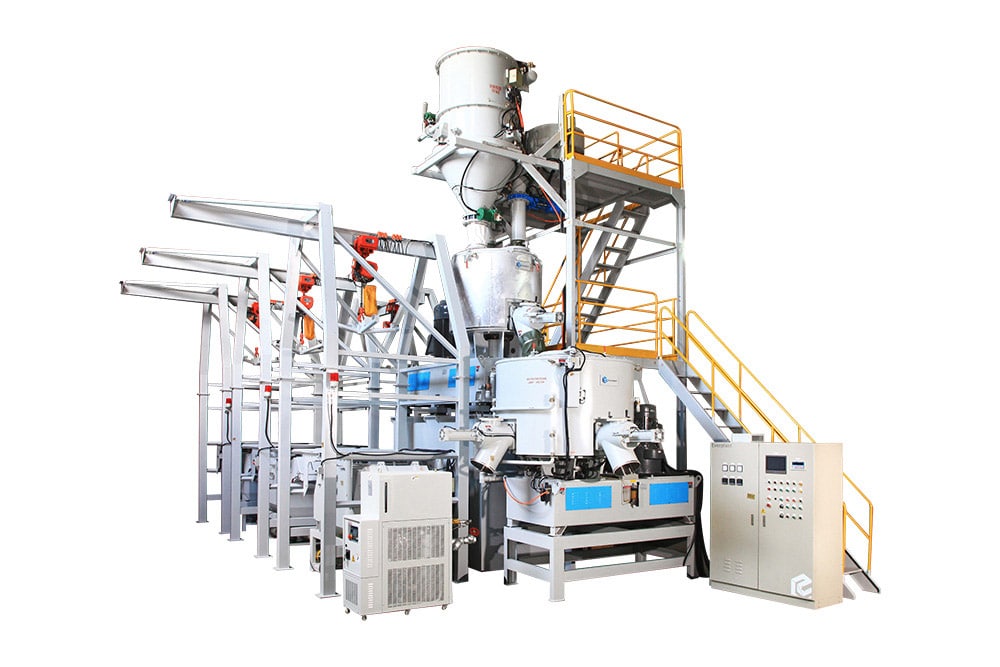
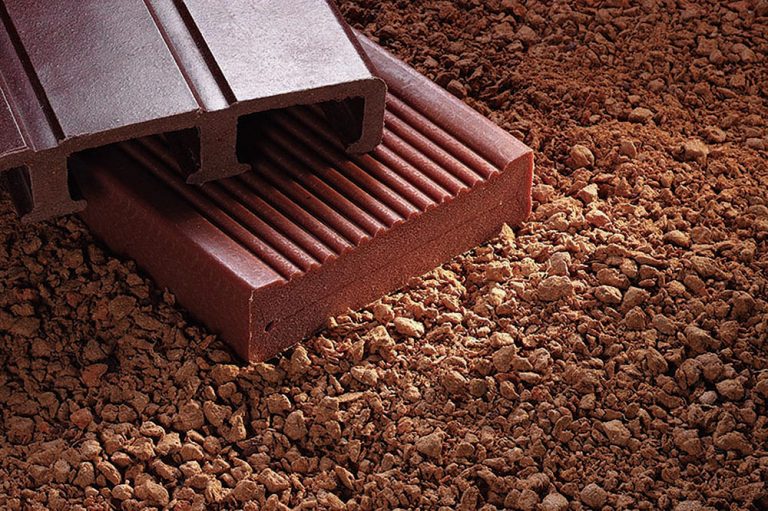
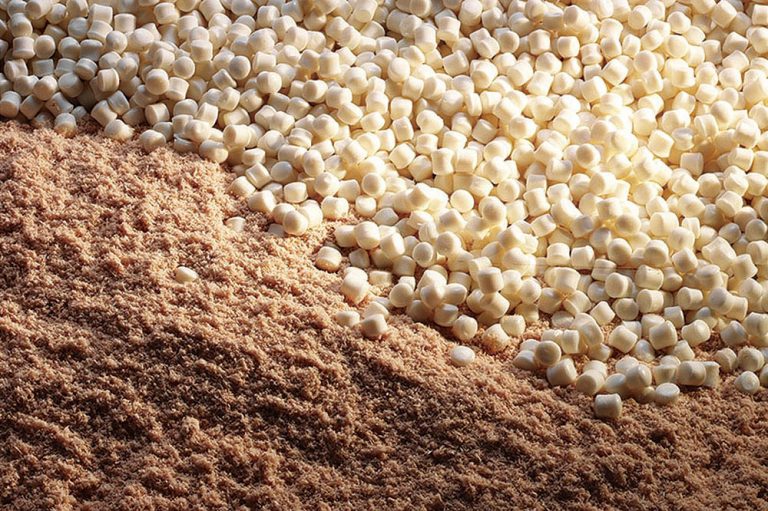
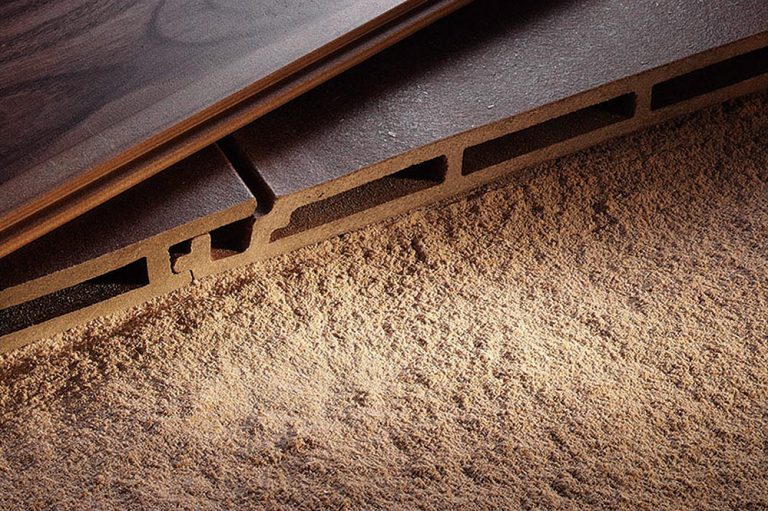

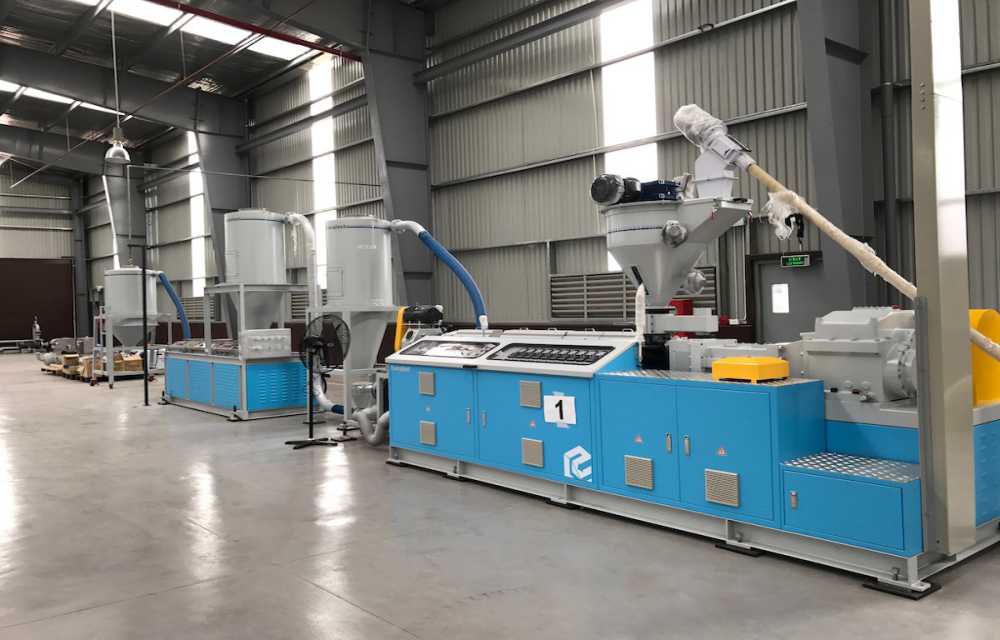
WPC Compounding Production Line
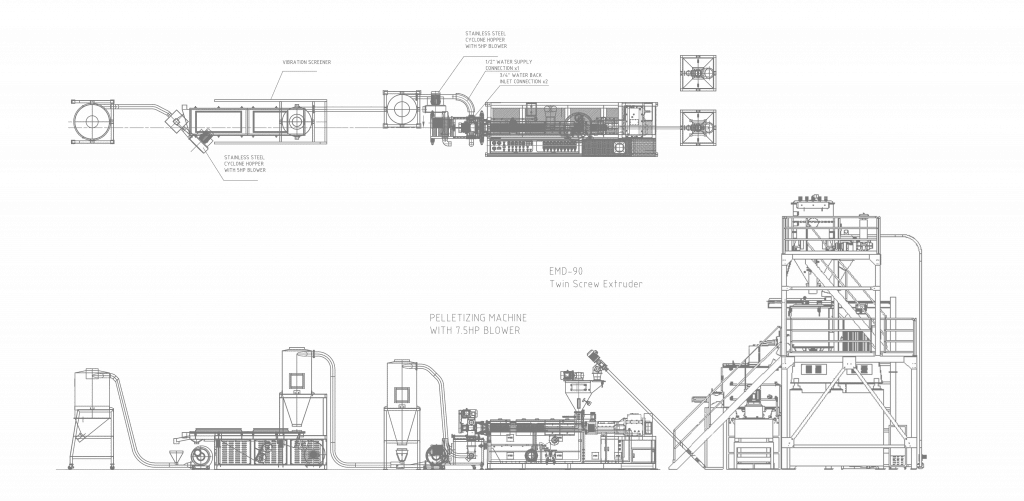
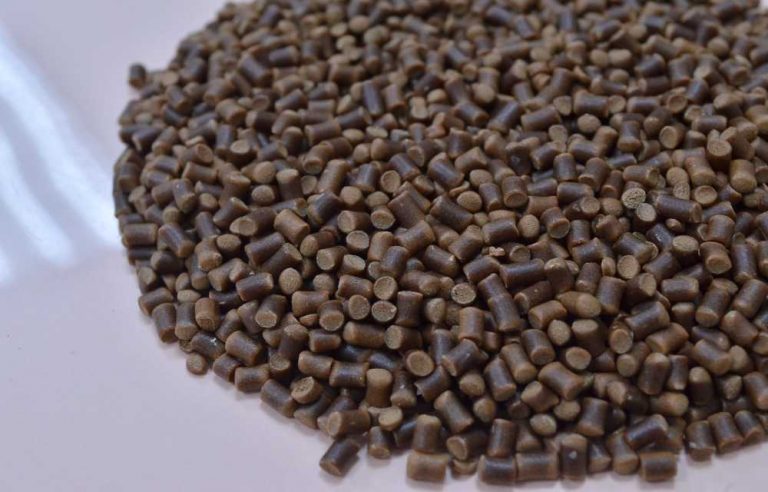
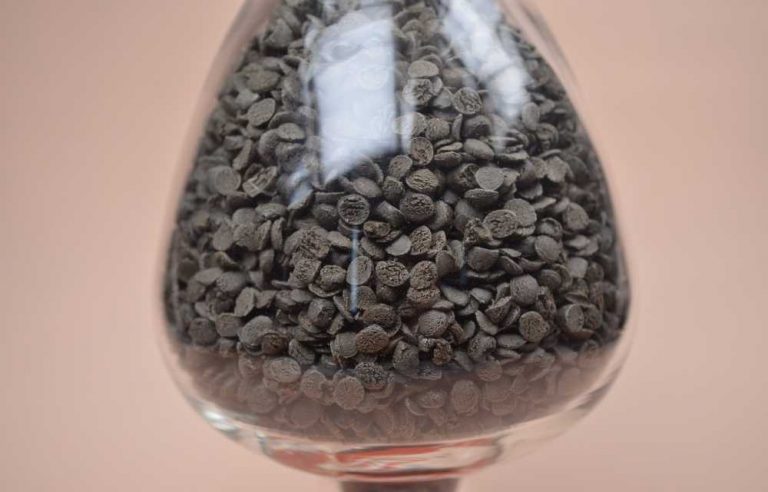
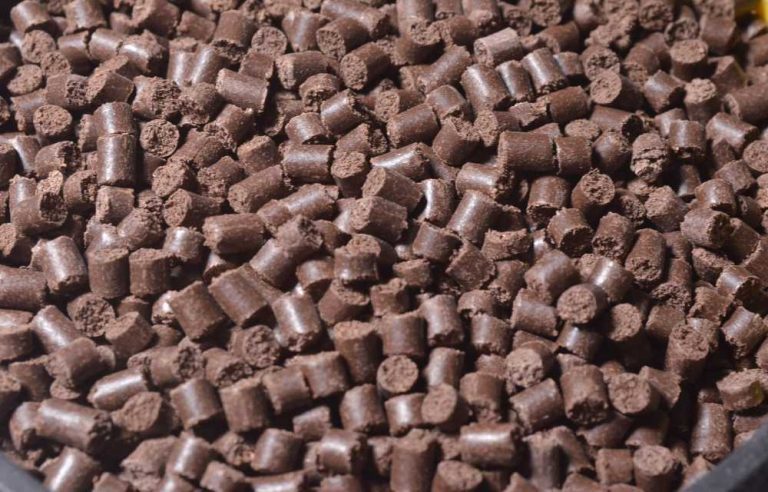
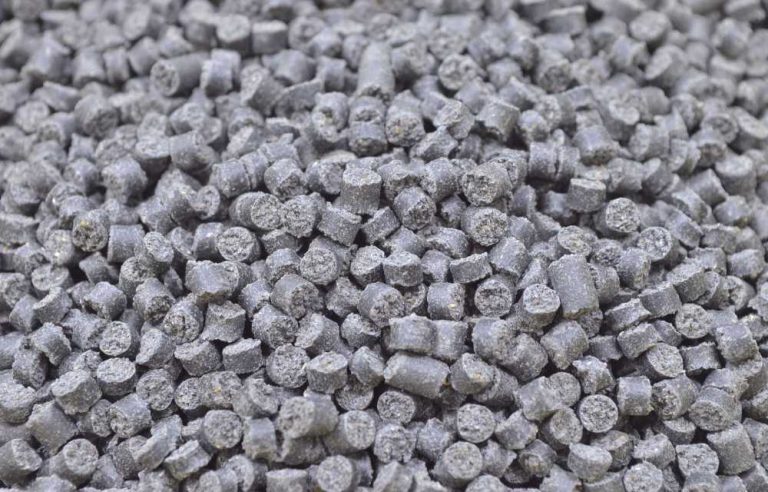
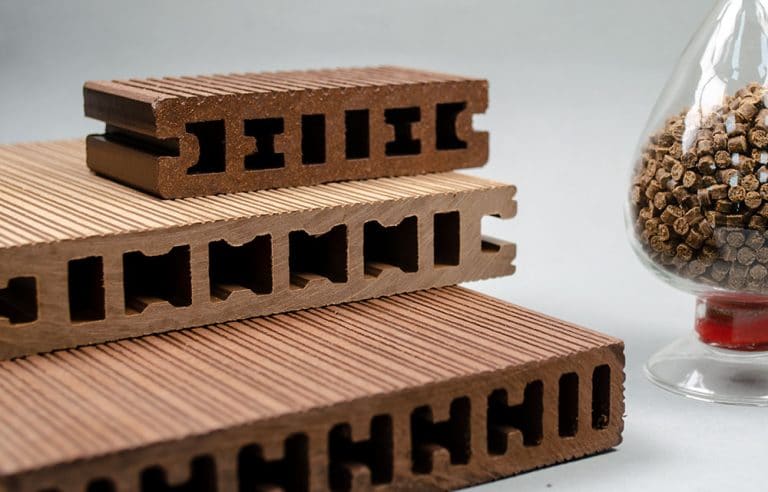
WPC Production Line
The use of natural fibers in extruded profiles is becoming increasingly popular. Attempts have been made to develop new features of finished wood-plastic composites (WPC), such as PP/PE resin mixing 40-80% natural fiber or PVC mixing 40-70% natural fiber. To meet the quality requirements, Everplast has developed a segmented twin screw extruder with special single screw extruder line as well as a parallel twin screw extruder with special single screw extrusion line combining tooling die head and all downstream equipment.
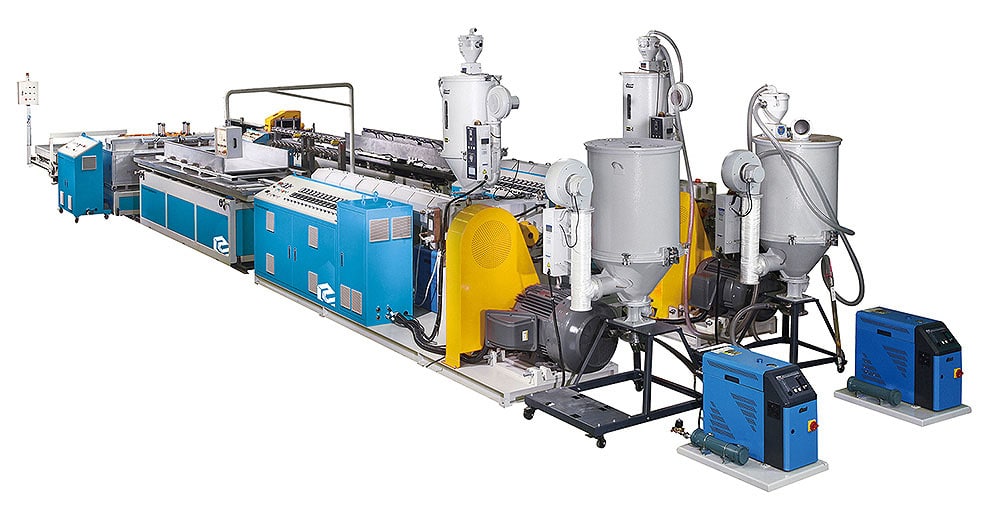
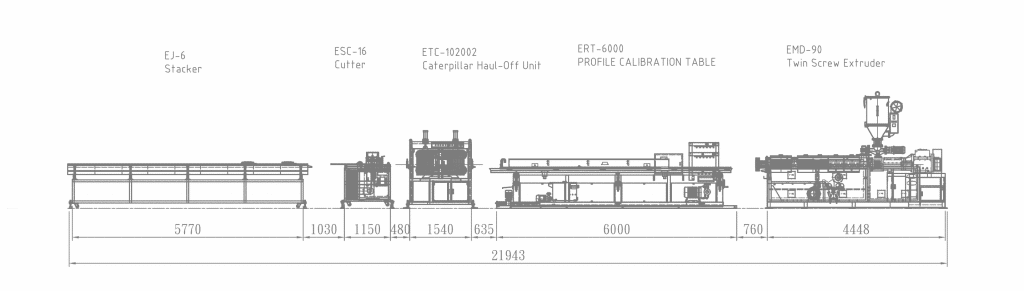
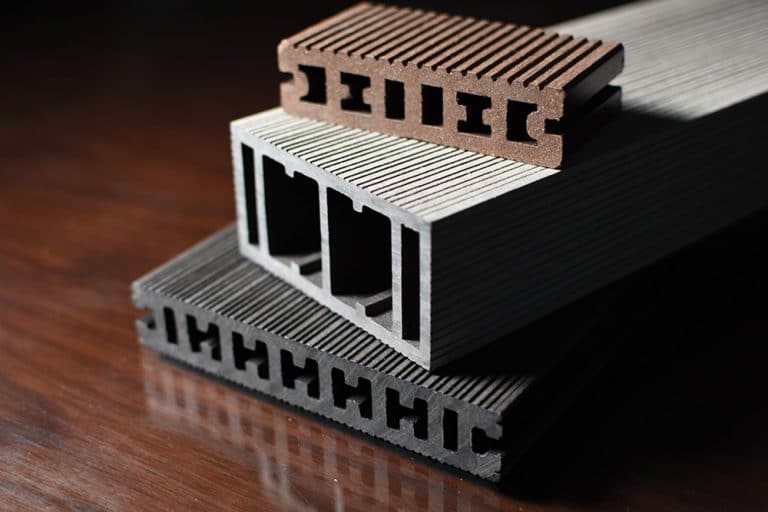
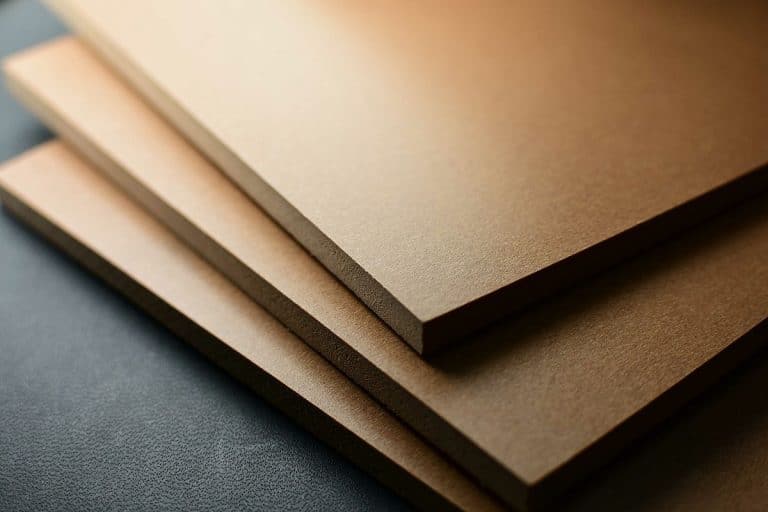
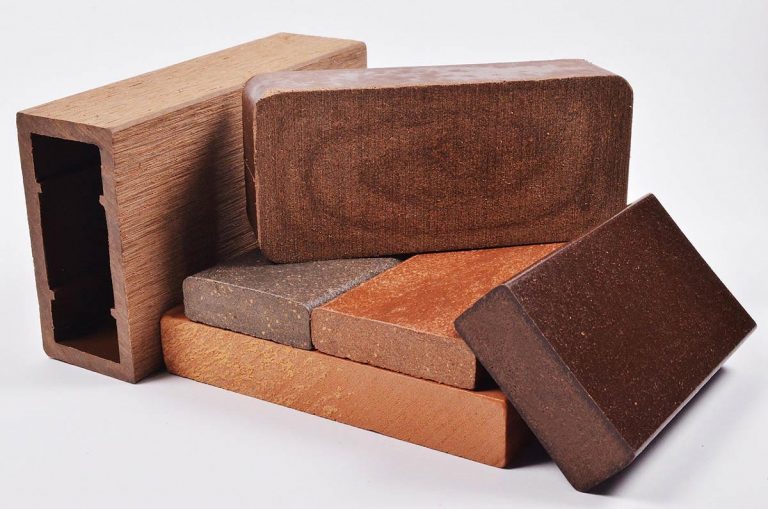
WPC Molds
The WPC profile mold design divides into hot extrusion molding and cold extrusion molding. The hot extrusion molding line speed is approximately 0.3~1 m/min. The special design of a sink insulation system is capable of increasing the production speed; as the high wood powder content reaches 60%, the cold extrusion molding technology can ensure that the center thermoplastic wood material does not penetrate through the skin layer. As a result of a slow production speed (0.3~1m/min), the rear end pulls without dragging the whole thing off.
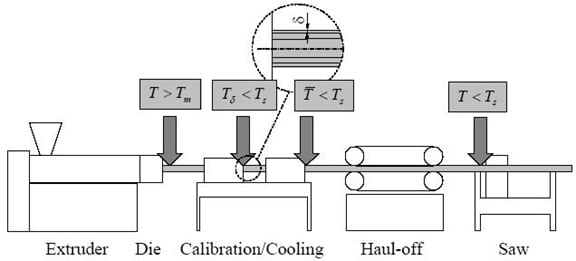
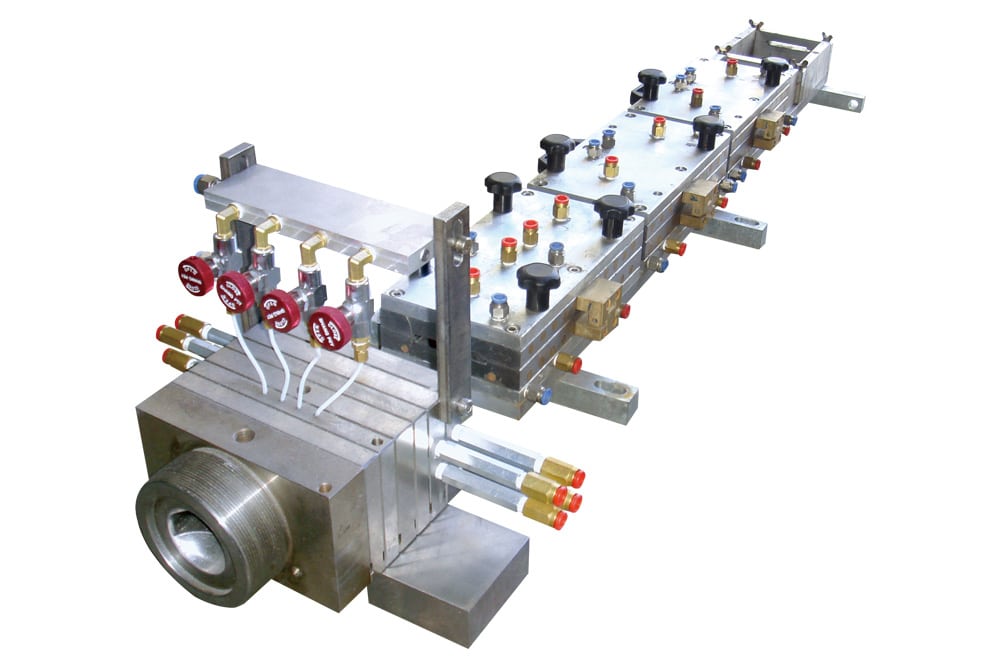
Hot extrusion molding: the average temperature of plastic mold is greater than the melting point (Tm). For the first sizing mold, the skin temperature (T) must be lower than the curing temperature (Ts), and the skin must have sufficient strength to avoid the central uncured plastic rupture in the cortex. Furthermore, the average temperature of the finalizing mold must be lower than the curing temperature (Ts) to avoid re-melting, and the cross-section temperature difference must be minimized to avoid residual stress. The temperature of the cutting section must be lower than the curing temperature.
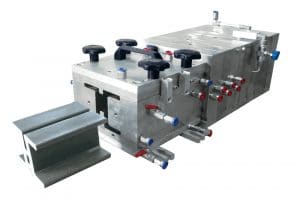
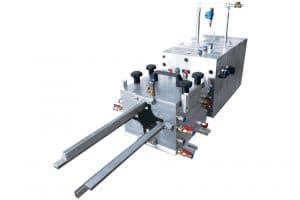
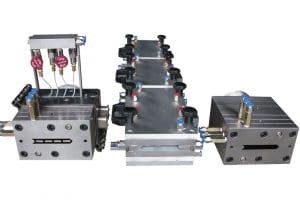
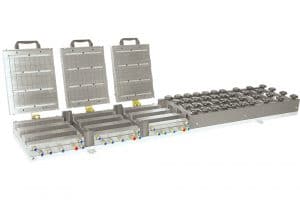
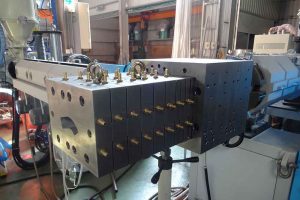
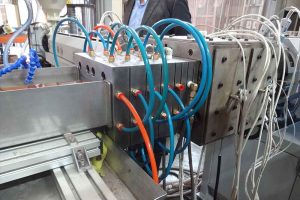
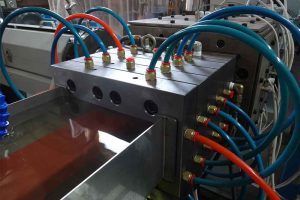
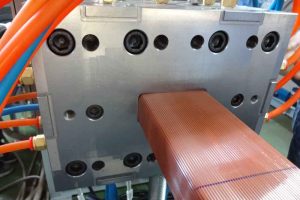
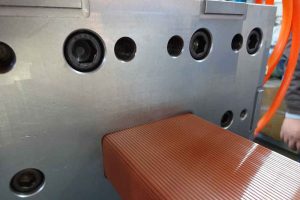
WPC Sanding Machine
Sanding machine, used to polish the finished surface of plastic wood, and the increase of roughness makes the product more realistic as well as reducing the slips. Everplast also provides other back-end processing needs, including printing machine, steel brush machines, calendar mill, etc.
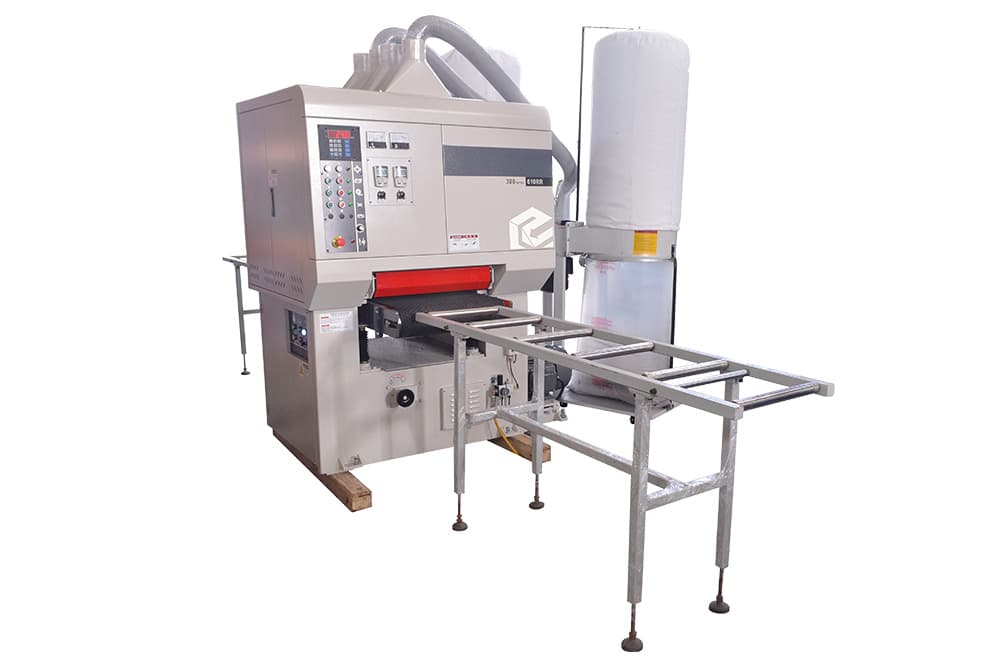
WPC Embossing Machine
To meet the customers’ needs, we offer a variety of embossed threads to make products more unique and aesthetically pleasing.
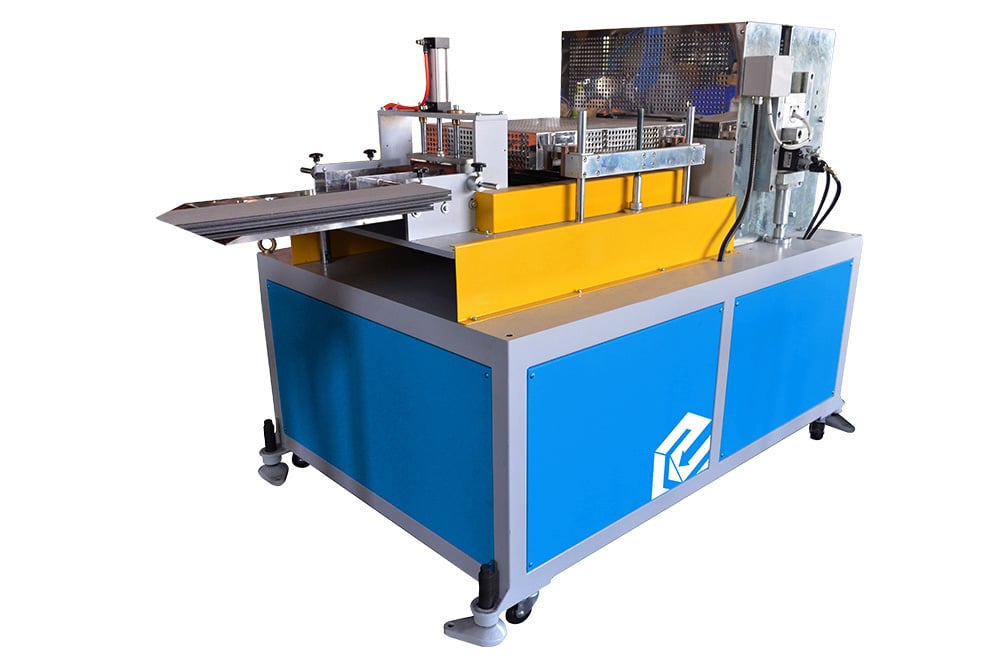
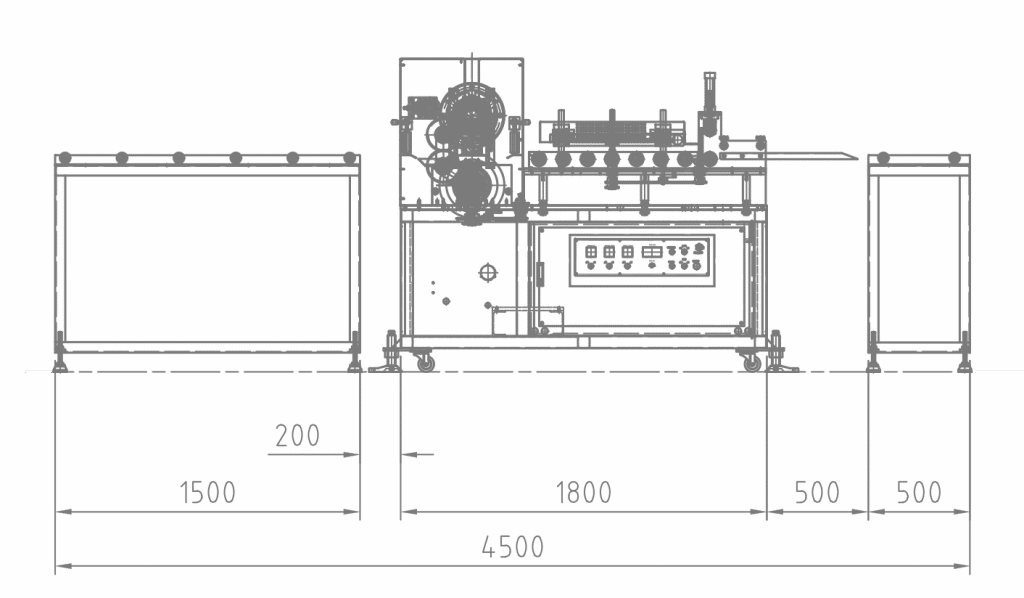
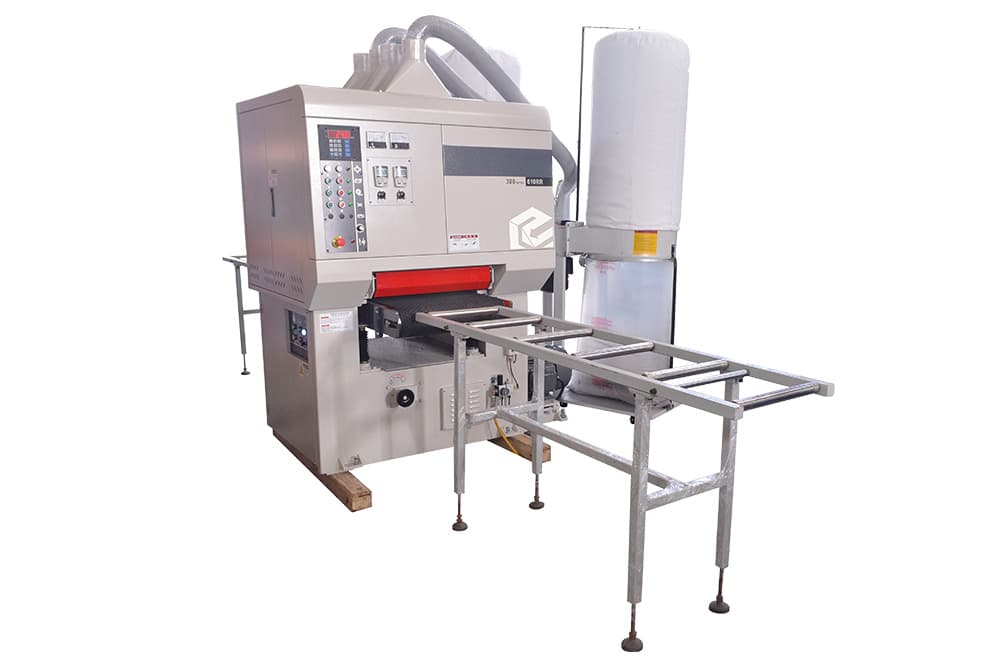
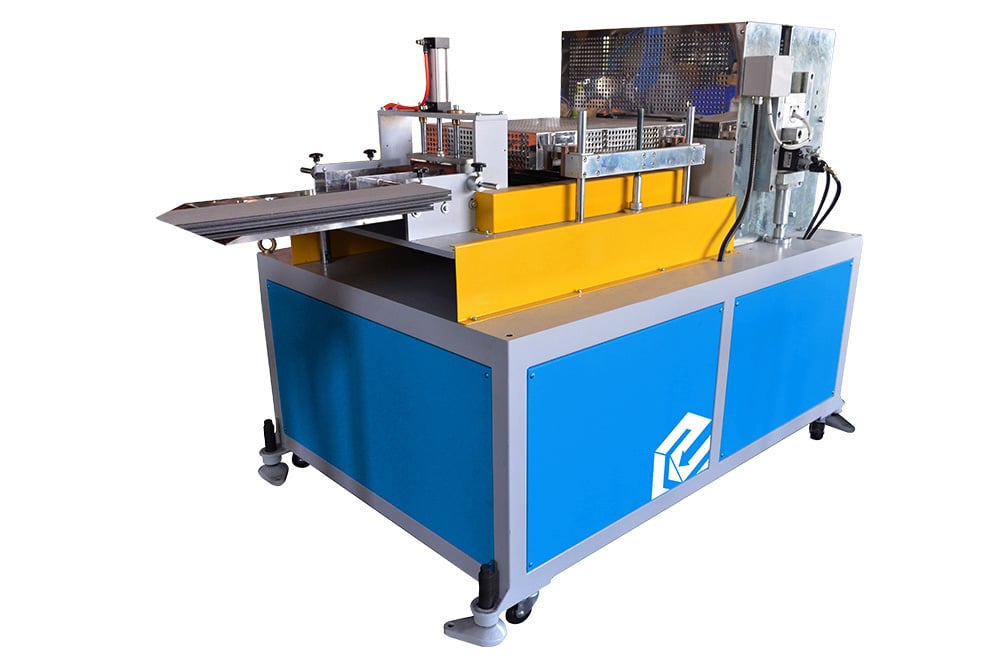
WPC Application
WPC divides into two parts: one being solid and the other being hollow. The inner surface of the hollow structure can produce a smooth and rough inner surface with the mold technology.
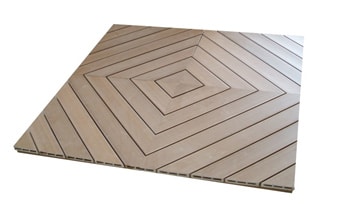
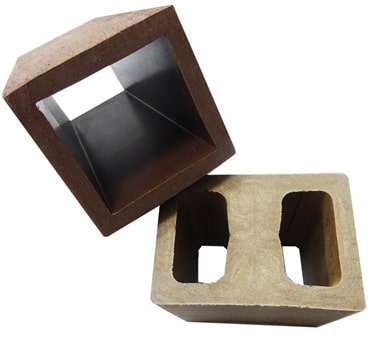
According to the plastic substrate, WPC divides into PVC, PE, PP, PS, and ABS, and even products of PBT and PET are in development. Even though PVC is inflammable, it still has environmental protection issues. PE plastic wood has a large consumption, however, the oily wax texture of the material has low heat resistance, poor foaming, poor printing performance, and a product shrinkage; PP plastic wood has a wax texture and can withstand high temperature. Although the secondary processing has a risk of cracking, the appearance and texture are identical to real wood, hence It can very well be done without post-production.
WPC Foaming Product
According to the foaming agent, WPC products divide into foamed and non-foamed WPC. After foaming, WPC can not only reduce weight but also can be processed by ordinary woodworking equipment, with wood cutting, sawing, adhering and nailing, hence easier to thermoform.

WPC products categorize into single-layered and co-extrusion. Traditional single extrusion WPC is lack of climate resilience and wear proof. Long-term outdoor exposure can cause tarnishing, crumbling, staining, mold growth, etc. However, the skin layer of a WPC co-extrusion product uses WPC recycling material or foaming to enhance climate resilience and the texture of the WPC products.
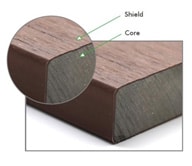
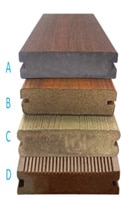
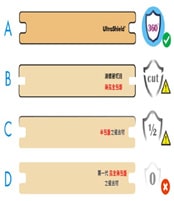
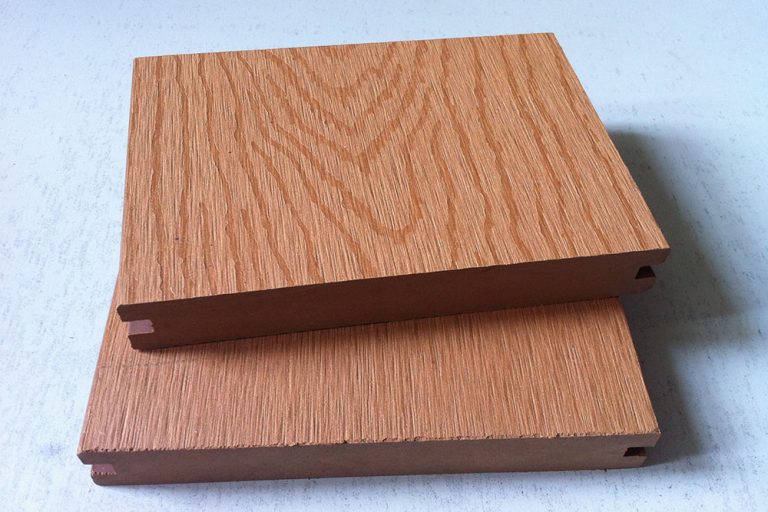
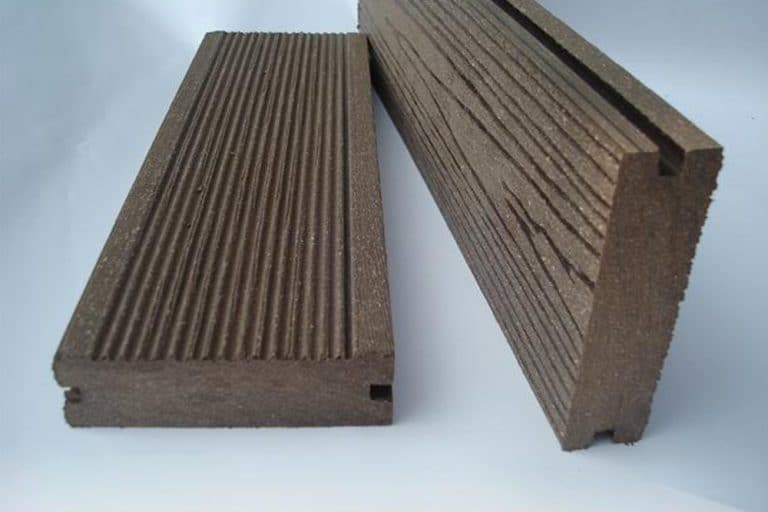
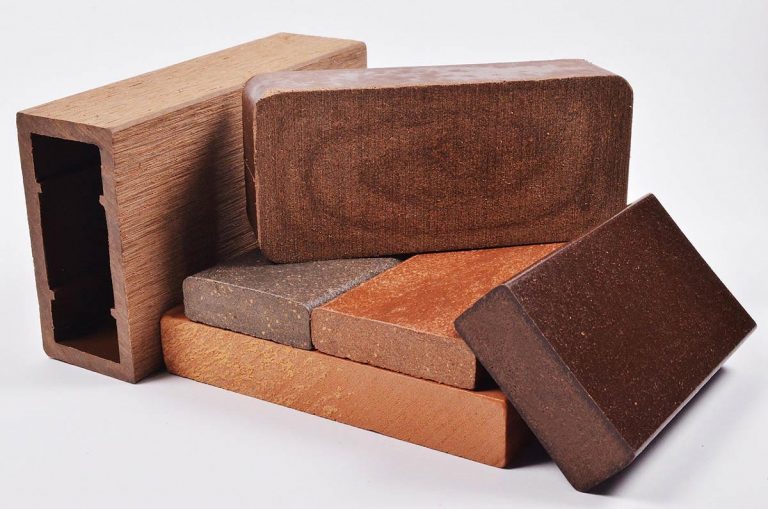
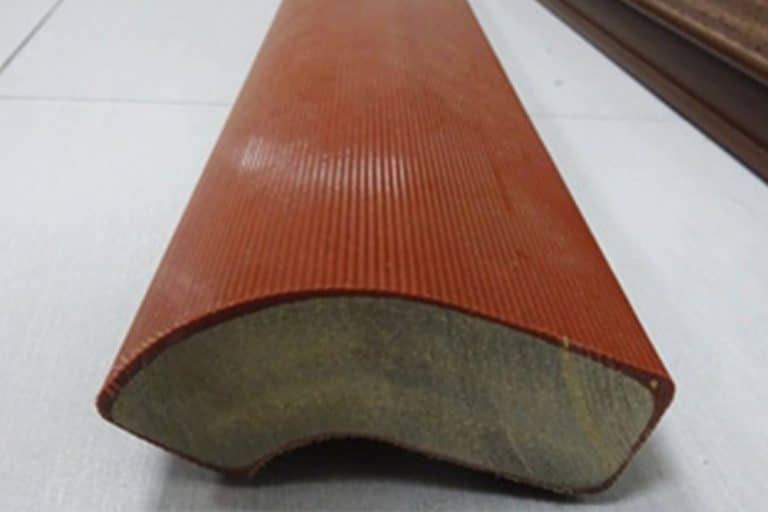
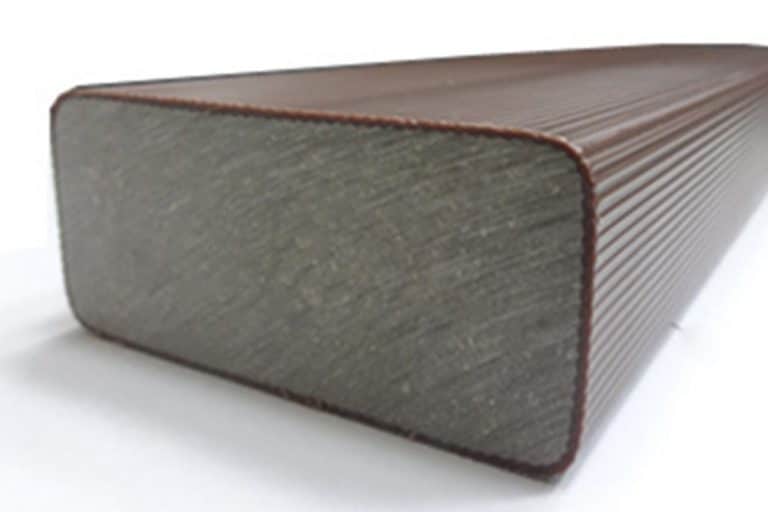
WPC Embossing Type
Surface treatment technology: sanding, embossing, coating, and thermal transfer. The surface of WPC floor is quite slick, in order to prevent slipping, the surface of the WPC floor needs processes through a sanding machine or a wire drawing machine; WPC floor is sanded and then embossed for improvement. Therefore, the wooden floor is non-slip and wear proof.
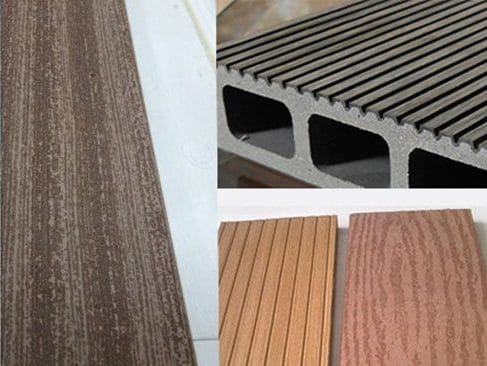
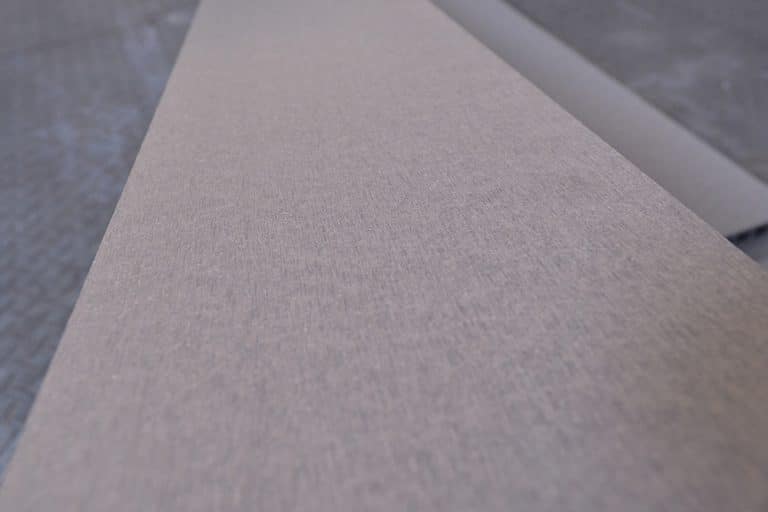
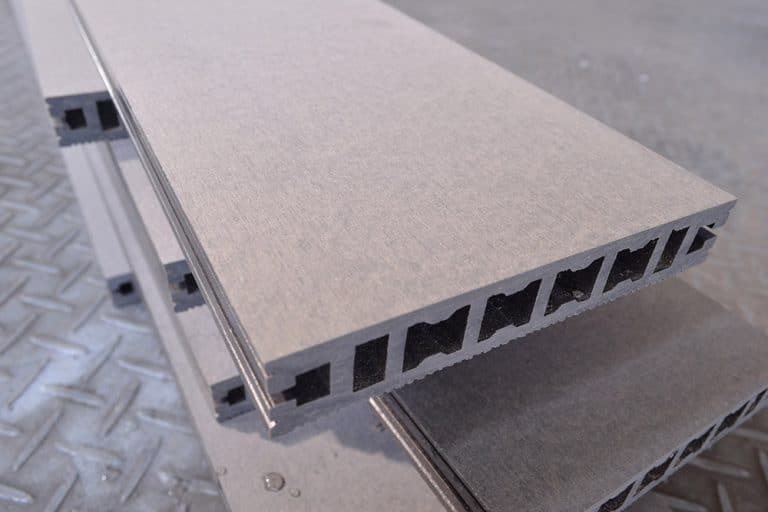
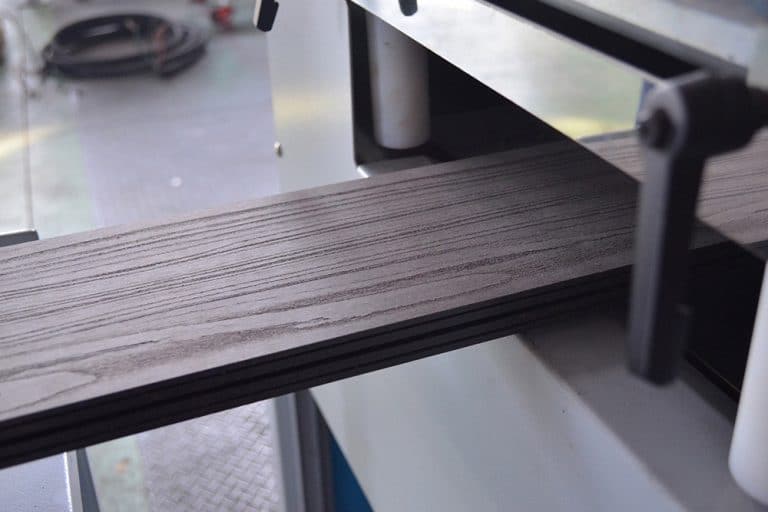
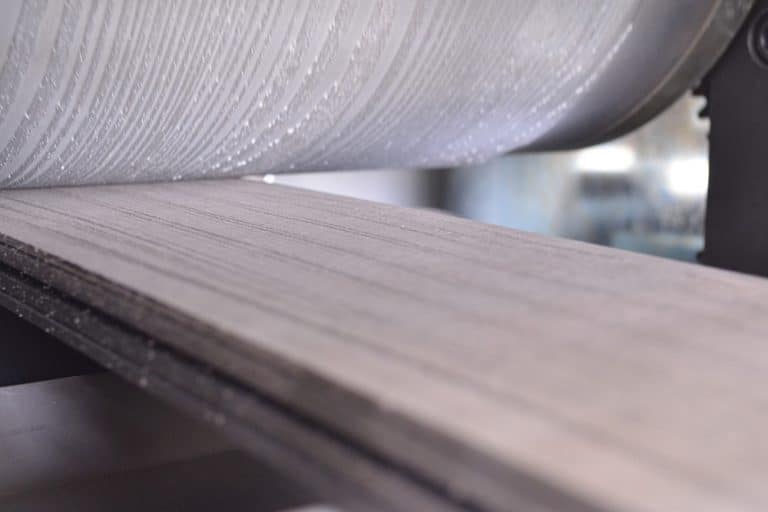
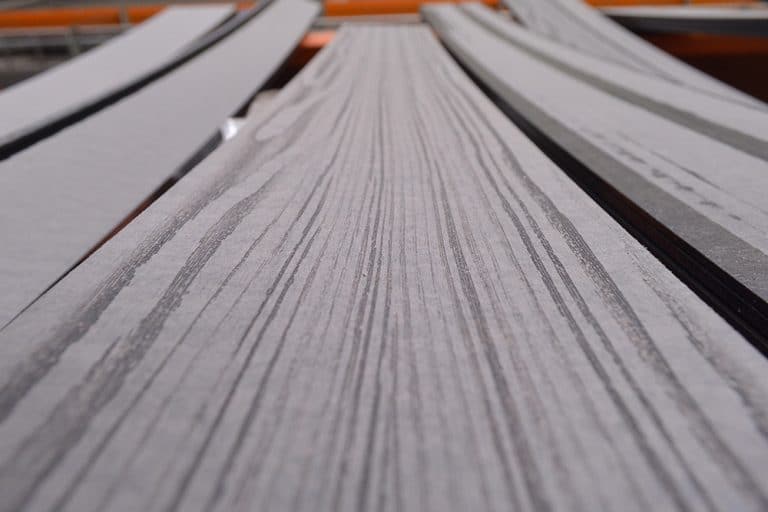
Send Products Inquiry to Us
To provide with better services, pleaser fill out the form below.